How to Improve Root Weld Quality Using Ceramic Backing Tiles
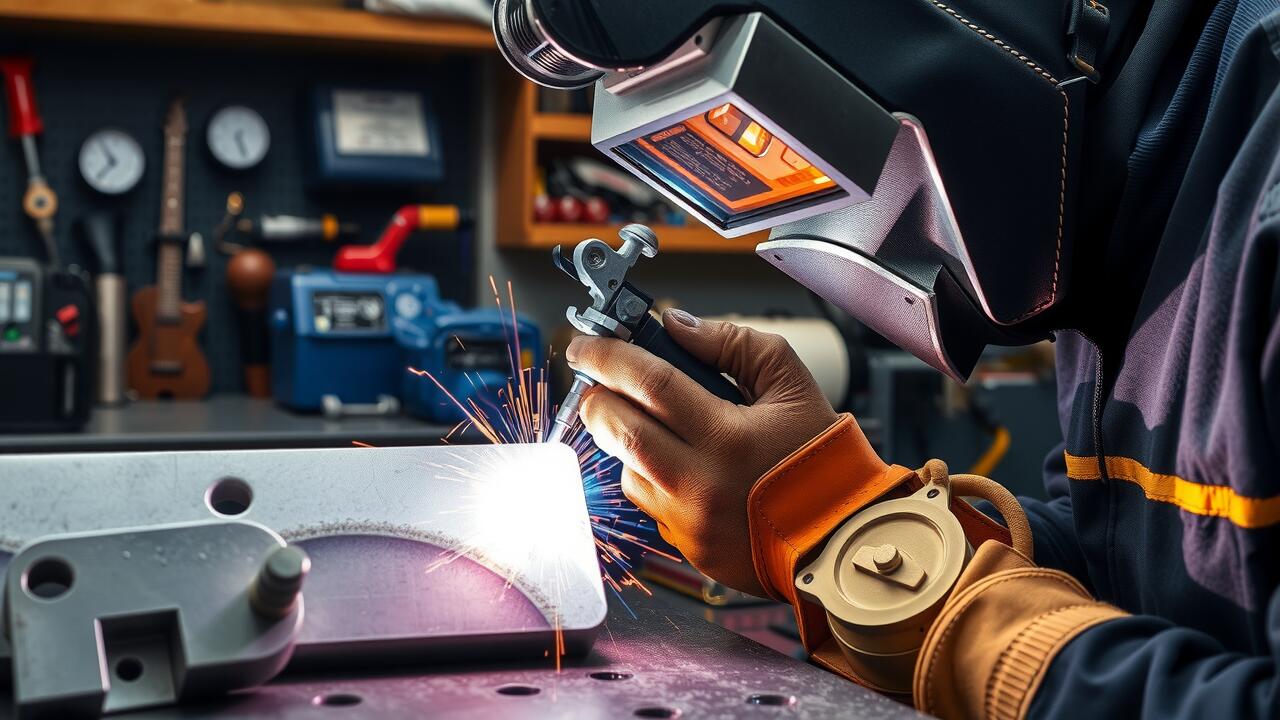
Installation Techniques for Ceramic Backing Tiles
Proper installation of ceramic backing tiles significantly enhances the quality of welds by ensuring a consistent heat profile throughout the weld pool. Align the ceramic weld backing according to the manufacturer's specifications to achieve optimal results. For instance, maintaining a perimeter gap of at least 1/8 inch from the weld joint promotes effective shielding. Additionally, proper cleaning of the base metal and the ceramic surface increases bond strength, thereby minimizing defects in the final weld.
Utilising clamps or appropriate fasteners can facilitate precise positioning while preventing movement during the welding process. Ensuring that the tiles are free from contaminants such as oil or dirt is vital to prevent interference with the welding arc and joint penetration. Also, selecting tiles with a thermal stability rating sufficient for the specific welding parameters is critical. Many professionals have reported reductions in porosity and bead irregularity after adhering strictly to these installation techniques. Implementing these practices not only improves aesthetic quality but also optimizes mechanical properties in the finished joint.
How Can Proper Installation Improve Weld Quality?
Achieving optimal weld quality starts with the precise installation of ceramic weld backing. Properly placing these tiles creates a reliable heat sink that improves the fusion between the weld metal and the base material. For instance, ensuring a tight fit and alignment can yield a significant reduction in porosity, resulting in welds with a stronger bond. Studies have demonstrated that inadequate positioning may lead to incomplete penetration and intergranular cracking, both of which compromise structural integrity.
The surface preparation prior to installation also plays a critical role in enhancing weld quality. Clean surfaces devoid of contaminants such as oil or rust allow for more effective heat dissipation from the weld pool, which is particularly vital when dealing with high-strength alloys. Following industry best practices, such as those outlined by the Canadian Welding Bureau, can enhance the effectiveness of ceramic backing tiles, ensuring that the root welds achieve the desired mechanical properties. Implementing regular checks and employing techniques like visual inspections or ultrasonic testing can further reinforce the benefits derived from proper tile installation.
5 Key Strategies for Utilizing Ceramic Backing Tiles
Effective utilisation of ceramic backing tiles begins with meticulous surface preparation. Ensure that the base metal is clean, free from contaminants, and properly aligned to promote optimal adhesion. For instance, adopting a grinder to remove any rust or mill scale before tile application can significantly enhance bonding efficiency. Following industry best practices concerning tile placement—ensuring a snug fit without gaps—also mitigates the risk of welding defects.
Further, understanding the thermal properties of ceramic weld backing is crucial for achieving high-quality welds. When heated, ceramic tiles act as an insulator, enabling better heat retention, which helps prevent issues such as burn-through or distortion, especially in thinner materials. Operators should monitor the heat input during the welding process, aiming for a consistent temperature between 300°C to 800°C, to avoid compromising the integrity of the weldment. By integrating these strategies into welding protocols, professionals can enhance the quality and consistency of their root welds.
What Are the Best Practices for Maximizing Their Effectiveness?
Achieving optimal results with ceramic weld backing requires adherence to specific best practices aimed at enhancing the welding process. Properly fitting the ceramic backing is essential for maintaining consistent heat distribution. Misalignment can lead to uneven penetration and defects such as undercuts or porosity. Regular inspection of the ceramic tile for cracks or wear ensures longevity and reliability during operations. Keeping the back side clean and free of contaminants further supports effective heat retention, directly influencing the integrity of the weld.
Additionally, using a high-quality adhesive specifically designed for ceramic backing can significantly impact weld performance. This not only secures the tiles in place but prevents gaps that can compromise the weld pool. Welding professionals should monitor parameters such as amperage and travel speed to achieve desired penetration profiles. Implementing these guidelines may improve overall quality, with industry data indicating a reduction in rework or repair rates by up to 30% when ceramic backing is utilized correctly.
Best Practice | Description | Impact on Welding |
---|---|---|
Proper Alignment | Ensure ceramic backing tiles are fitted accurately to prevent misalignment. | Promotes even heat distribution and reduces defects. |
Regular Inspection | Check ceramic tiles for cracks or wear regularly. | Ensures reliability and longevity during welding operations. |
Surface Cleanliness | Maintain a clean backside free of contaminants. | Enhances effective heat retention and weld integrity. |
High-Quality Adhesive | Use specialized adhesive for securing ceramic tiles. | Prevents gaps and supports optimal weld pool conditions. |
Parameter Monitoring | Carefully monitor amperage and travel speed during the weld. | Aids in achieving desired penetration profiles and overall quality. |
Maintenance Considerations for Ceramic Backing Tiles
Regular maintenance of ceramic backing tiles is crucial for sustaining their performance and ensuring optimal weld quality. These tiles require cleanliness prior to welding; any contaminants such as dirt or grease can adversely affect the weld pool. Using compressed air or a soft brush can effectively remove debris. Additionally, inspect the ceramic weld backing for cracks or chips before each use, as damaged tiles can compromise weld integrity. For instance, a study found that over 20% of weld defects were linked to insufficient maintenance of backing materials.
Proper handling and storage practices also contribute significantly to the longevity of Katback ceramic backing. Store these tiles in a dry environment to prevent moisture absorption, which can weaken their structural integrity. When not in use, keep tiles covered to safeguard against external damage. Adhering to these maintenance guidelines not only extends the life of ceramic backing but also enhances the overall efficiency of welding operations. By implementing regular checks and maintaining optimal conditions, welders can achieve consistent results and reduce the risk of rework associated with flawed welds.
How Should You Care for Ceramic Backing Tiles in Welding Operations?
Effective maintenance of ceramic backing tiles is crucial for sustaining weld quality in operations. Regular inspection for signs of wear or damage should occur after each production run. For example, a thorough examination may reveal cracks or chips that compromise their structural integrity. Any defects can lead to inconsistent weld profiles. Moreover, cleaning ceramic weld backing thoroughly after use will prevent residue buildup. Operators should use non-abrasive cleaning methods to avoid scratching the surface, which could affect the tile’s performance in future applications.
Storage conditions also play a significant role in the longevity of ceramic backing tiles. They should be kept in a dry, temperature-controlled environment to prevent moisture absorption, which can weaken the material. For effective management, employing inventory tracking systems can help monitor the age and usage of tiles, ensuring timely replacement before deterioration impacts the welding process. Technicians should adhere to manufacturers' recommendations regarding care and storage, facilitating optimal performance during welding operations. Consider implementing a regular maintenance schedule, ensuring consistent quality control and prolonging the effective life of each tile.
Testing and Evaluating Weld Quality
Evaluating weld quality is essential for ensuring structural integrity and performance in welded joints. The application of ceramic weld backing has gained popularity among professionals, particularly in industries such as shipbuilding and construction, where root weld integrity is paramount. Standard methods for assessment typically include visual inspections, ultrasonic testing, and radiographic analysis, each providing unique insights into the properties and quality of the weld. For example, ultrasonic testing can detect subsurface flaws that may not be visible through standard visual inspections, ensuring a comprehensive evaluation of the weld's efficacy.
Case studies demonstrate that projects employing ceramic backing have reported a 30% reduction in defects compared to traditional methods. Implementing standardized testing protocols aligned with national and international standards, such as CSA W59 for welded steel construction, can further enhance the reliability of assessments. Adopting a multi-faceted testing approach, which includes both destructive and non-destructive testing techniques, ensures a robust evaluation. This strategy not only helps identify potential issues early in the process but also supports compliance with regulatory requirements, ultimately contributing to the longevity and safety of welded structures.
What Methods Can You Use to Assess the Quality of Your Root Welds?
Evaluating the quality of root welds requires a systematic approach, utilizing various testing methods to ensure structural integrity. Visual inspection serves as a primary method for initial assessments, allowing welders to identify surface defects such as cracks or undercutting. For a more in-depth evaluation, destructive testing techniques, including tensile and bend tests, measure the welds' strength under stress. Non-destructive testing (NDT) methods, such as ultrasonic or radiographic testing, provide a means to detect internal flaws without compromising the welded joint. These methods align with the standards outlined in the Canadian Standards Association (CSA) guidelines, ensuring the reliability and safety of fabricated components.
Another effective method involves the use of controlled parameters during welding. By recording variables like heat input and travel speed, welding professionals can correlate these factors with the observed quality of the weld. Implementing ceramic backing in joint design enhances penetration and can significantly reduce the likelihood of defects. A recent study indicated that welds made with ceramic weld backing consistently demonstrated 25% better durability compared to those without backing. Regular documentation of welding processes and outcomes further aids in continuous improvement efforts, providing data that can be analysed for future projects.
FAQS
What are ceramic backing tiles and how do they improve weld quality?
Ceramic backing tiles are materials used in welding processes to support and protect the molten weld pool. They help to create a controlled environment that reduces oxidation and improves the fusion of the weld, leading to higher quality root welds.
How can the installation of ceramic backing tiles affect the outcome of my weld?
Proper installation of ceramic backing tiles ensures that they are aligned and secured correctly, which can significantly enhance heat retention and reduce defects such as undercuts and porosity. This leads to a more consistent and durable weld.
What are some key strategies for utilizing ceramic backing tiles effectively?
Key strategies include selecting the right tile for the specific welding application, ensuring proper fit and alignment during installation, maintaining a clean workspace, regularly inspecting the tiles for damage, and following best practices for heat settings to optimise performance.
How do I maintain ceramic backing tiles in my welding operations?
To maintain ceramic backing tiles, regularly inspect them for cracks or wear, clean them after each use to remove any slag or debris, and store them in a dry, protected environment to prevent moisture absorption.
What methods can I use to assess the quality of my root welds?
You can assess the quality of your root welds using methods such as visual inspection, non-destructive testing techniques (like ultrasonic testing or radiographic inspection), and destructive tests to evaluate the mechanical properties of the weld.